A cosa serve il cemento di scoria e come fare una soluzione?
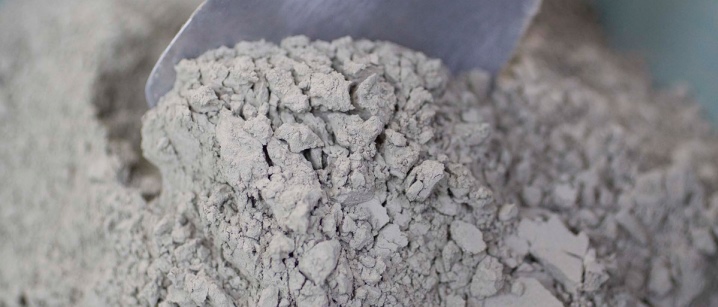
Il cemento di scoria è una sostanza idraulica ottenuta artificialmente con un pronunciato effetto astringente. È in qualche modo analogo al cemento Portland. La sua caratteristica principale è che contiene scarti dell'industria metallurgica finemente macinati, ovvero scorie.
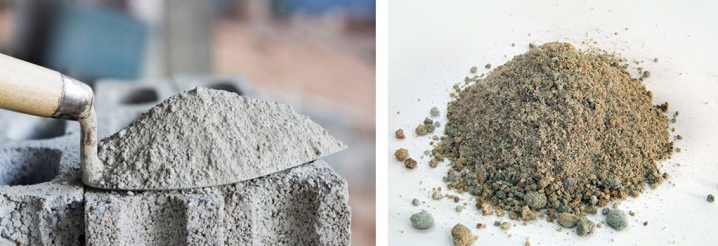
Cos'è e come si produce
La scoria granulata d'altoforno si ottiene come rifiuto nel processo di fusione del metallo ferroso. Ha proprietà intrinseche che si applicano alla costruzione generale del cemento Portland, ma ci sono differenze. Sotto forma di prodotto finemente macinato, è attivo nella manifestazione di proprietà astringenti, interagendo con l'acqua e anche con i prodotti di idratazione dei minerali di tipo clinker (quelli che fanno parte del cemento Portland semplice).
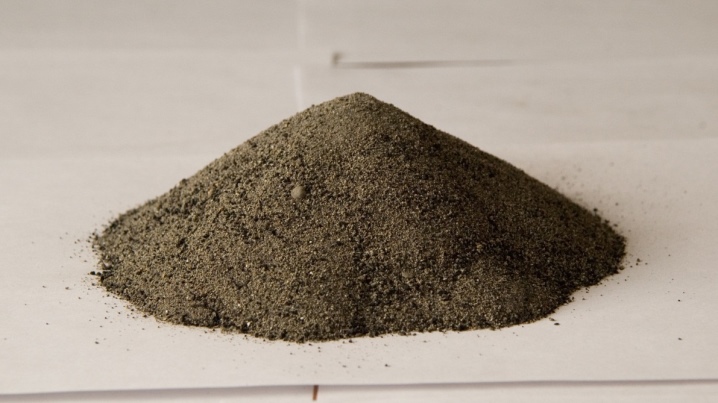
I componenti del cemento di scoria sono:
- clinker: non contiene più del 6% di magnesio;
- scorie: fino all'80%, la quantità ottimale di questo componente dipende dai requisiti proposti per il prodotto legante;
- gesso - sia naturale puro che con un contenuto di fosforo, fluoro e boro, non più del 5% di gesso dovrebbe rappresentare l'intera massa.
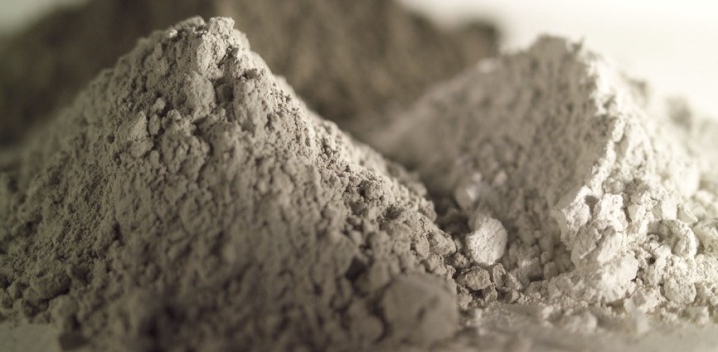
Il cemento con scoria è considerato un legante, il cui uso non è limitato a nessuna direzione. Alla domanda sul perché, in linea di principio, le scorie vengono aggiunte al cemento, si può rispondere come segue: una soluzione concreta, che include cemento e scorie, ha un basso costo. E se confrontiamo il prezzo di una soluzione concreta basata sul cemento Portland standard con cemento con scorie, il secondo sarà finanziariamente più redditizio. Cioè, non è migliore in linea di principio, ma più redditizio con caratteristiche quasi uguali.
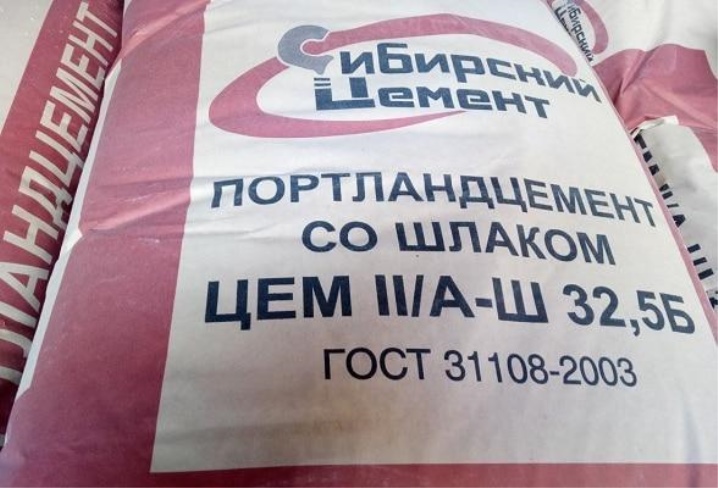
A proposito, sulle caratteristiche. Anche la miscela di scorie e cemento è buona perché la temperatura di rilascio del calore in essa sarà relativamente bassa.
E anche questo prodotto:
- ha una maggiore resistenza all'influenza delle acque (solfate e dolci);
- caratterizzato da una maggiore resistenza al calore;
- ha un'elevata resistenza al gelo (con la condizione di utilizzare la tecnologia di cottura a vapore del calcestruzzo prefabbricato).
In generale, la conclusione è che il caso aziendale standard decide nella scelta dei materiali.
Il costo del prodotto descritto non comprende i notevoli costi di estrazione, macinazione e lavorazione.
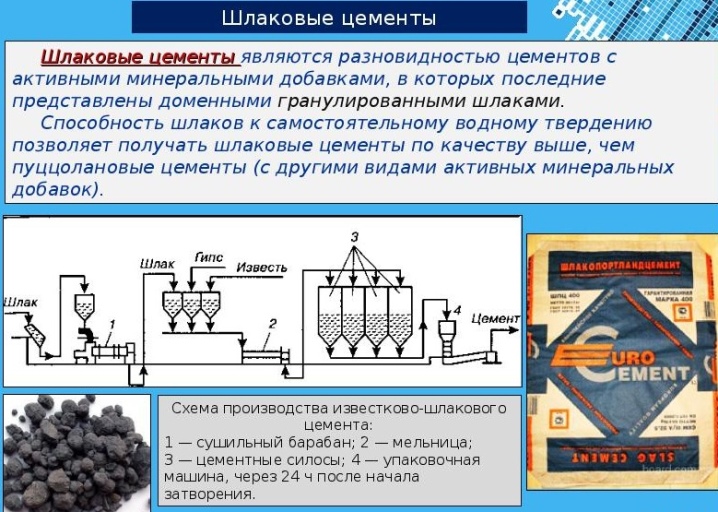
Il materiale è ottenuto da clinker di cemento Portland, scorie, argilla e calcare. Il fatto è che nella produzione del cemento è importante la composizione chimica del materiale e non la sua struttura fisica. Pertanto, devi scegliere la fonte con grande cura. Nella produzione di questo cemento è possibile utilizzare scorie d'altoforno sia basiche che acide.
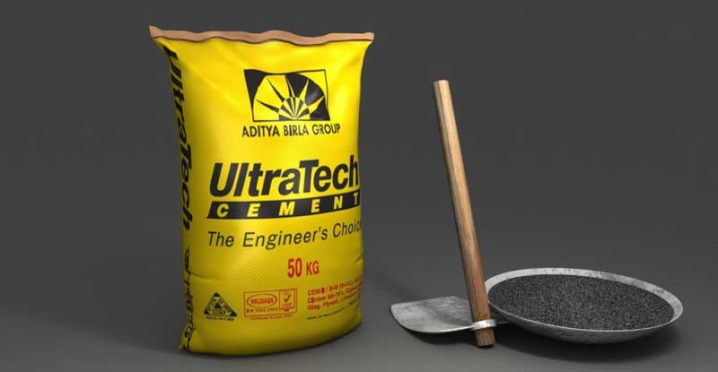
A proposito, le scorie stesse possono essere granulari e non granulari, ma tuttavia le prime vengono utilizzate molto più spesso e il punto è, ancora una volta, nella componente economica.
Ma c'è un altro motivo per usare scorie granulari: lo stesso processo di produzione del prodotto finale con scoria non granulare diventa notevolmente più complicato. Ma quelle scorie che vengono aggiunte al prodotto dopo la cottura vengono granulate senza fallo.
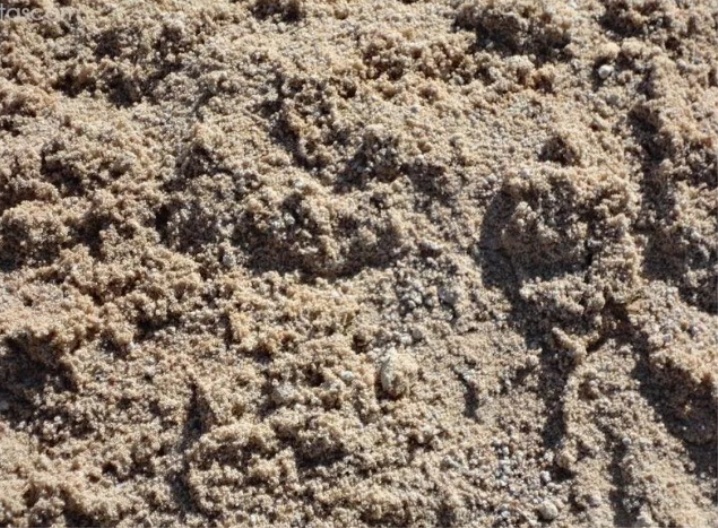
Attenzione! La percentuale di scoria nel cemento non deve superare 60.
Come ha dimostrato la pratica, cemento in fusione con scoria significa ottenere un materiale resistente, piuttosto affidabile, poco durevole, ma abbastanza convincente per molti scopi. Ecco perché questo prodotto è utilizzato così attivamente nella costruzione a più piani.Con il suo aiuto, vengono realizzate lastre e cinture corazzate, strutture subacquee e strutture vicine all'acqua, aiuta anche nell'isolamento termico, durante la colata di alcuni prodotti in costruzione. Cioè, con questo prodotto si possono raggiungere obiettivi costruttivi completamente diversi: con alta efficienza, fattibilità economica e grandi opportunità.
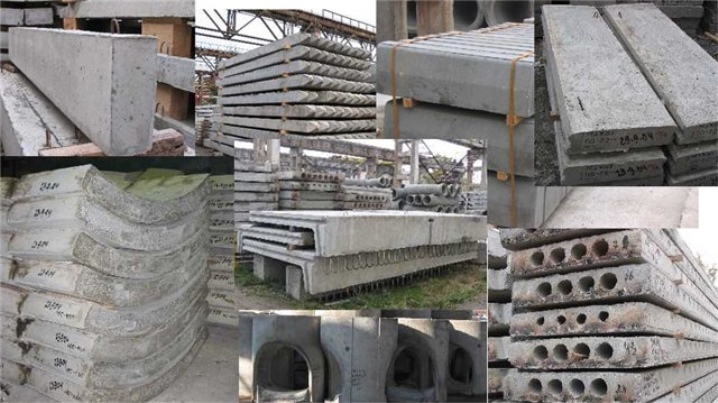
Panoramica delle specie
ShPC (cemento portland di scorie) è diviso in due tipi principali: indurimento normale e indurimento rapido.
Indurimento normale
Le proprietà del materiale sono descritte in GOST 10178-85. Il materiale differisce in quanto maggiore è la quantità di scorie, più a lungo si indurirà la miscela. Meno calore sarà prodotto dalla reazione di idratazione.
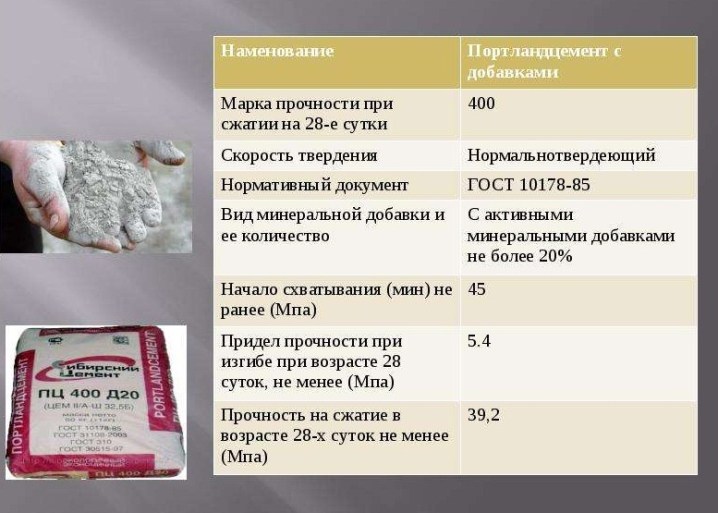
Dopo la solidificazione, la scoria non deve reagire con l'acqua, motivo per cui la miscela viene spesso utilizzata per creare strutture con elevata umidità.
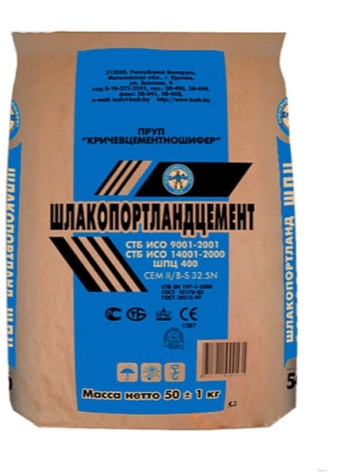
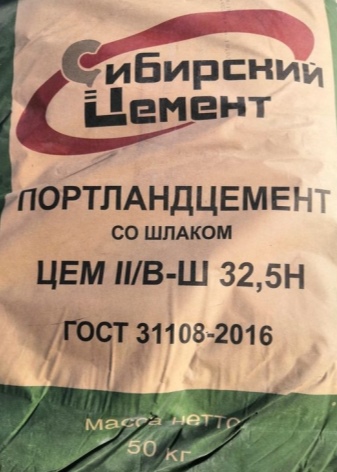
Indurimento rapido
A questo materiale vengono aggiunti speciali additivi per accelerare il processo. Gli additivi possono essere di eziologia minerale e vulcanica, cioè cenere o pomice.
Vale la pena ricordare che la durata di conservazione del cemento di scoria è inferiore a quella di una semplice malta cementizia secca.
Dal momento della spedizione del prodotto, non devono trascorrere più di 45 giorni prima che il materiale venga utilizzato. Ma usare un prodotto scaduto significa correre molti rischi. Perde le sue proprietà prestazionali, e in modo significativo.
Sorge spesso la domanda se le differenze tra cemento Portland e cemento Portland scorie siano significative. Sì, sono significativi, se non altro per il fatto che il primo costerà molto più del secondo. E anche il cemento Portland acquisisce forza di finitura più velocemente di ShPC (indurisce completamente dopo 3 settimane). In linea di principio, non ci sono scorie nel cemento Portland, c'è clinker e composizione minerale con additivi-acceleranti. Ma la densità dell'SPC è inferiore a quella del cemento Portland, così come il suo peso sarà anche inferiore, più precisamente il peso delle strutture che ne fanno parte.
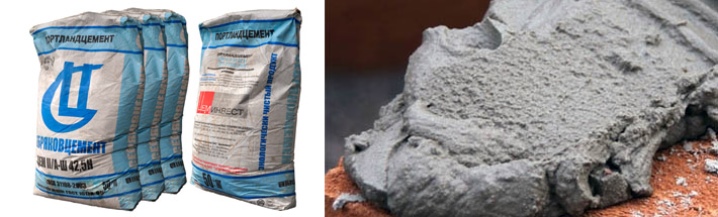
Per cosa è adatto
Questo materiale è particolarmente richiesto se è necessario costruire calcestruzzo, nonché strutture in cemento armato che saranno costantemente in contatto con l'ambiente acquatico (ad esempio, ShPC M400 contiene almeno il 21% di materiale granulare). Il prodotto ha proprietà di resistenza sufficienti per questo. Viene utilizzato per produrre malta cementizia di alta qualità, per realizzare pannelli per pareti e produrre miscele secche. Questo tipo di cemento non perde nulla dello stesso marchio M500, ma questo marchio è un cemento classico.
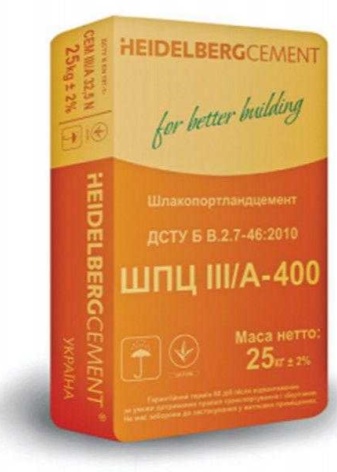
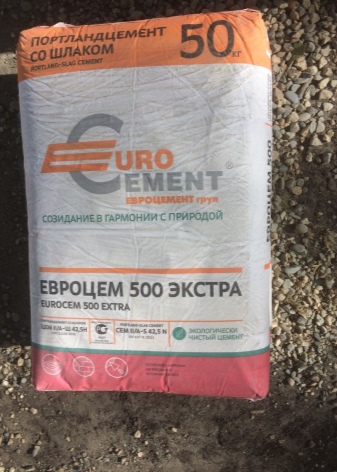
Ancora una volta, anche qui è riuscita la costruzione di pareti e soffitti con rinforzo - cemento con l'aggiunta di scorie. Viene utilizzato attivamente in cantieri di grandi dimensioni e la sua leggerezza lo aiuta in questo (se confrontato con silicato e ceramica, gli SPT, ovviamente, non sono una lanugine, ma vince in modo significativo).
Perché il peso è così importante: la questione è nel carico sulle parti della fondazione e sulle parti strutturali della struttura: sarà ridotto.
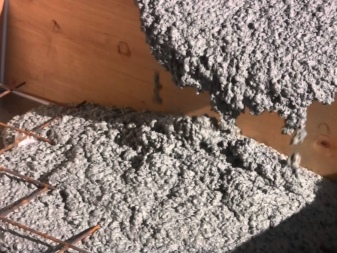
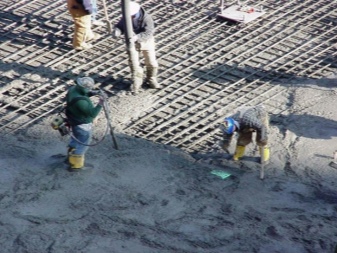
Il muratore ha la capacità di realizzare lastre di dimensioni imponenti utilizzando cemento con scorie - si risparmia tempo di installazione e denaro. E il trasporto di pannelli SPT di solito non causa problemi.
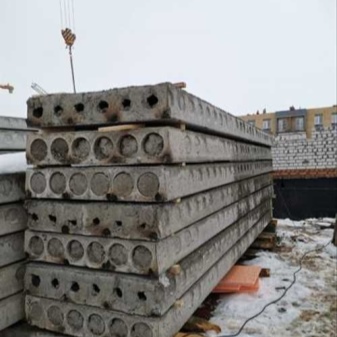

Dove viene utilizzato il materiale - aree di applicazione:
- costruzione di elementi monolitici e prefabbricati (intendendo sia edilizia privata che industriale);
- fabbricazione di strutture che richiedono il più rapido indurimento possibile della base;
- pavimentazioni stradali con presa rapida della miscela;
- costruzione di cavalcavia e ponti;
- produzione di lastre per lastricati e pietre per lastricati;
- costruzione bassa con le sue diverse fasi: dal riempimento delle pareti al lavoro con le fondamenta;
- sostituzione di malte per intonaci e murature.
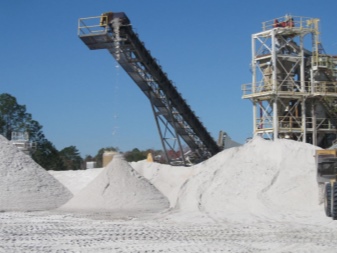
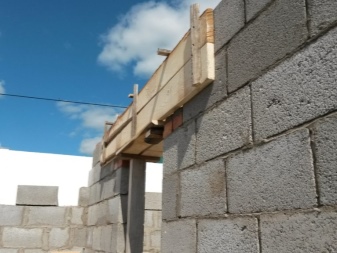
Il materiale viene utilizzato attivamente nella produzione di cinture rinforzate, che si trovano spesso anche nelle costruzioni a più piani. Il materiale funziona alla grande in combinazione con i riscaldatori convenzionali come mezzo di isolamento termico.La classe 50 è considerata la scelta migliore per il rinforzo, la classe 35 è per la costruzione di elementi portanti, la classe 25 è più che adatta per le piccole strutture non più importanti, la classe 10 è utilizzata nell'isolamento termico.
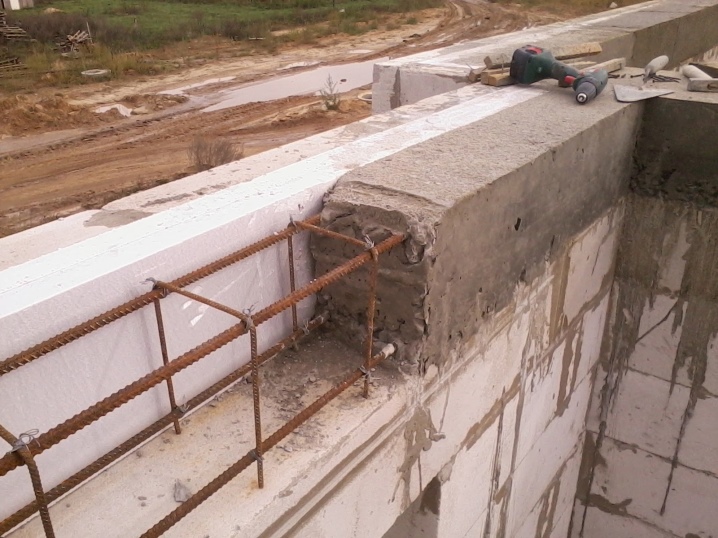
Proporzioni di applicazione
Se si decide di rifinire le superfici interne con questo prodotto, si preferisce la scoria a grana grossa. Sarà necessario per una soluzione di circa 6 parti. Le restanti 4 parti cadranno su scorie granulari a grana fine. Ma in questo caso, qualsiasi cemento viene utilizzato per il calcestruzzo.
Per finire la facciata esterna, è necessario diluire la soluzione in diverse proporzioni: utilizzare 7 parti di scoria a grana grossa per 3 parti di scoria a grana fine.
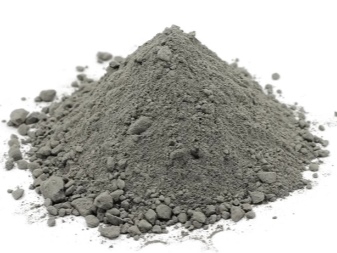
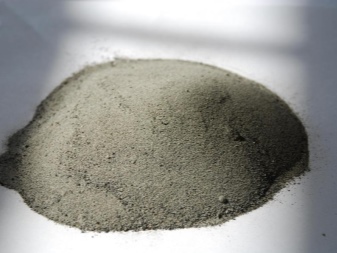
Il cemento deve essere preso di alta qualità con un'elevata resistenza alle influenze esterne.
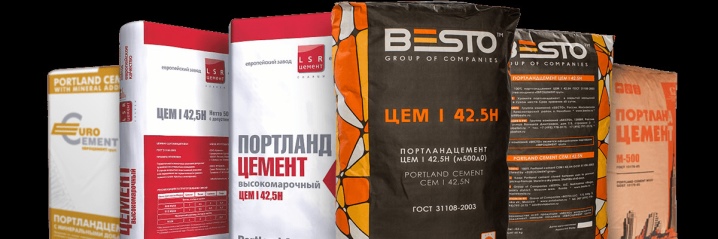
Per un versamento efficace, nonché nel caso in cui la riserva di tempo non si esaurisca, è possibile prelevare scorie non granulate. Naturalmente, la solidificazione di tale miscela sarà lenta, ma la qualità del rivestimento supera una miscela con una composizione granulare. Su tali crepe non si formano presto, ma su un pavimento pieno di scorie granulari, possono apparire dopo un paio d'anni.
Per finire la parte esterna della fondazione sporgente, è necessaria anche una scoria granulare. Più grande è la superficie da rifinire, più grandi dovrebbero essere i granuli nella scoria: questo è il rapporto. Funziona anche il feedback.
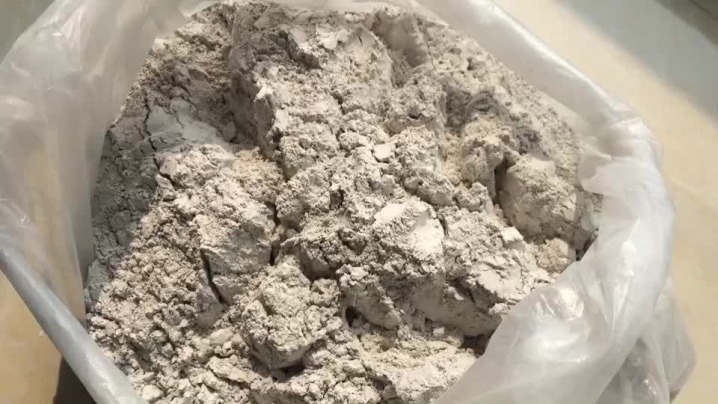
Come rendere concrete le scorie:
- poche ore prima del lavoro, la scoria deve essere inumidita con acqua - questo influisce sulla durabilità del calcestruzzo, che si forma nel corso delle azioni successive;
- i componenti sono miscelati nel rapporto sopra indicato (scegliere quello giusto in base allo scopo), tutto è accuratamente miscelato;
- dopo aver aggiunto acqua alla composizione, deve essere nuovamente impastata per ottenere uno stato omogeneo dell'impasto;
- per ottenere un grado medio di calcestruzzo, vengono utilizzate 4 parti di scoria (meno spesso 5) e 2 parti di cemento a 2 parti di sabbia;
- è indispensabile utilizzare correttamente il prodotto finito, questo deve essere fatto entro un'ora e mezza;
- se è necessario ridurre ulteriormente il costo della soluzione, il cemento può essere combinato con la calce in proporzioni da 3 a 1.
Le proporzioni sono indicate sulla confezione con la miscela.
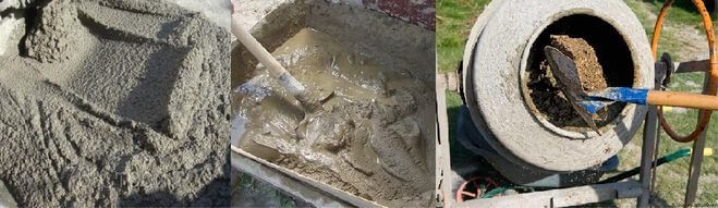
Il materiale ha ovviamente molti vantaggi, soprattutto per quei lavori edili dove prevale l'economia. Ma presenta anche degli svantaggi, che in alcune situazioni possono superare i vantaggi. Ad esempio, il cemento con scoria mostra una certa "capricciosità" alle cadute termiche. E sebbene sia considerato resistente al gelo, non può essere utilizzato a lungo in condizioni di bassa temperatura. Il materiale, infine, prescrive un'attenta manutenzione della struttura in caso di caldo: dovrà essere regolarmente inumidita e ricoperta di polietilene.
Finora, le miscele di calcestruzzo e i blocchi di costruzione con SHPC non vengono utilizzati molto attivamente e sono spesso realizzati in condizioni di fabbrica e nella costruzione vengono utilizzati sotto la supervisione di specialisti esperti. Tuttavia, il prodotto non può nemmeno essere definito un materiale molto raro. Probabilmente, ci si dovrebbe aspettare un ammodernamento nella produzione di questo legante idraulico.
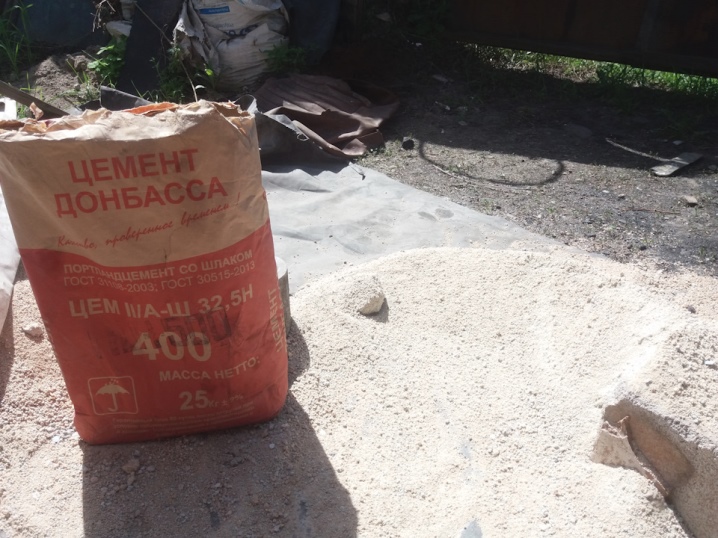
Una panoramica dettagliata dell'uso del cemento di scoria nel prossimo video.
Il commento è stato inviato con successo.