Caratterizzazione e applicazione di scorie metallurgiche
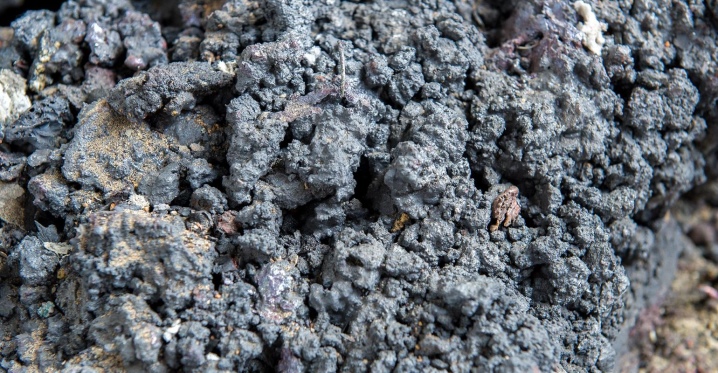
La scoria metallurgica trova la sua applicazione come sottofondo stradale e in altri campi di attività. La sua composizione e densità, le caratteristiche di produzione sono di particolare interesse per l'industria. Vale la pena parlare più in dettaglio di cosa è nella metallurgia, come viene utilizzato.
Cos'è?
Ci sono molti sottoprodotti rimasti dalla fusione di metalli ferrosi e non ferrosi. La scoria è il principale prodotto di scarto. È un prodotto di decomposizione del minerale, può avere una composizione eterogenea, proprietà e caratteristiche diverse. La scoria metallurgica si ottiene alla pari delle ceneri rimaste dopo la fusione dell'acciaio e della ghisa. Rimane in produzione dopo la lavorazione, richiede successivo smaltimento o riutilizzo come materiale autonomo.
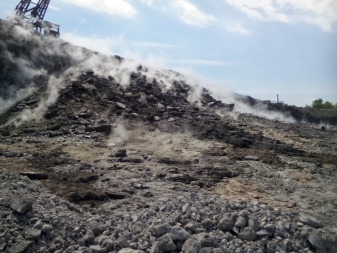
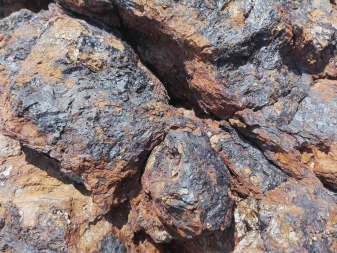
Le scorie metalliche sono prodotti di lavorazione ad alta temperatura. È un rifiuto di tipo silicato con una struttura multicomponente. Per molto tempo le scorie sono state semplicemente smaltite, non di particolare interesse. Tutto è cambiato nella seconda metà del XX secolo. Da quel momento in poi, i rifiuti della metallurgia iniziarono ad essere utilizzati attivamente nell'edilizia, nell'industria agricola e nella posa delle reti stradali.
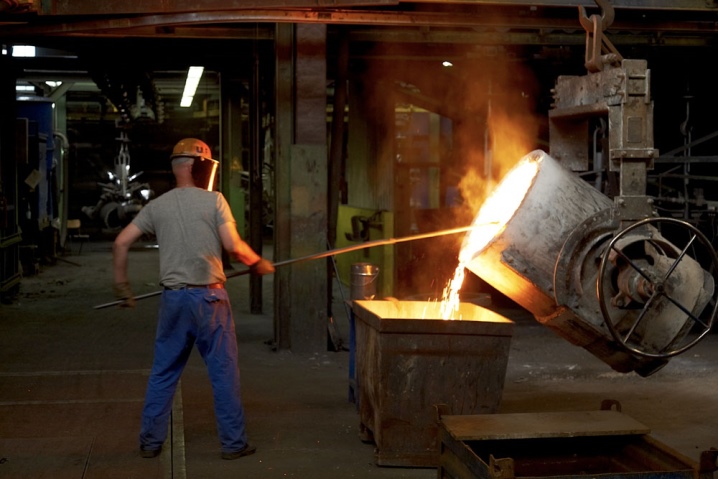
Composizione e proprietà
La composizione della scoria metallurgica non è uniforme. Infatti è una lega chimica di ossidi, che occupa dal 90 al 95% del volume. Il resto sono solfuri, solfati, composti alogeni. A seconda del contenuto di ossidi, le scorie sono suddivise in basiche (fino all'1%), monosilicati (1%), bisilicati (2%), acide (fino al 3%).
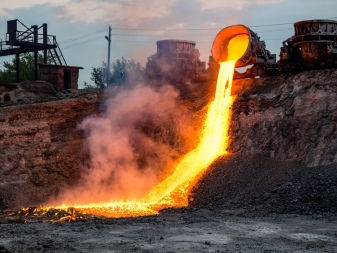
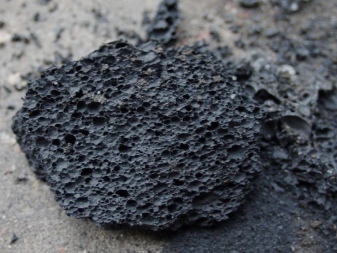
Elenchiamo il resto delle caratteristiche.
- Peso specifico del cubo. Sono 0,7-1,9 tonnellate per un prodotto sfuso e per un prodotto in pezzi - 0,7-2,9 tonnellate.
- Classe di pericolo. Il grado IV è stabilito per tutte le scorie metallurgiche. Ciò significa che i rifiuti metallurgici sono dannosi per l'ambiente e richiedono un corretto smaltimento e riciclaggio.
- Densità. Le sue prestazioni vanno da 750 a 1100 kg/m3.
- Produzione per 1 tonnellata di metallo. Per i metalli ferrosi va da 100 a 700 kg. La produzione moderna prevede l'uso di diversi processi di fusione dei metalli. In un altoforno, la media è di 80 kg / t, in un forno a focolare aperto - circa 30 kg / t, con una tecnologia di conversione - non supera i 18 kg / t. La metallurgia non ferrosa produce fino a 200 tonnellate di scorie per 1 tonnellata di metallo.
Tutti questi indicatori sono presi in considerazione nell'ulteriore utilizzo dei rifiuti dell'industria metallurgica.
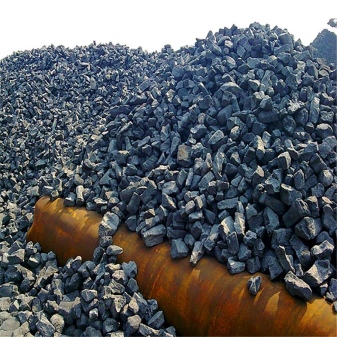
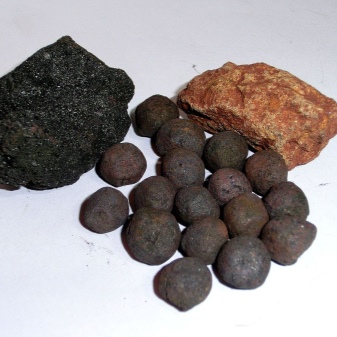
Caratteristiche della produzione
Secondo il metodo di produzione, le scorie nella metallurgia sono divise in diversi gruppi. In un impianto il trattamento dei rifiuti avviene contemporaneamente ad altri processi. Ad esempio, la separazione della scoria del convertitore nella produzione dell'acciaio viene effettuata nel processo di soffiaggio del metallo ferroso fuso. Tutte le inclusioni estranee vengono ossidate e quindi rimosse.
Quando si fondono metalli ferrosi, viene utilizzato il metodo prevalentemente a cupola. Si tratta di forni a tino originariamente utilizzati nella produzione della ghisa. Il metodo ha un'elevata efficienza, a differenza del trattamento in altoforno, non modifica la composizione chimica della lega. La scoria scende attraverso uno speciale foro per il rubinetto.
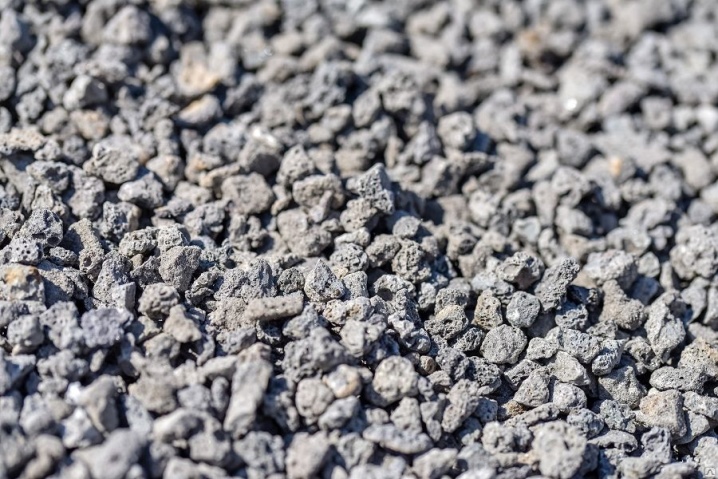
Altri tipi di forni sono utilizzati per fondere metalli non ferrosi. La scoria risultante, ricoperta da un film, viene lavorata in un modo speciale.
Per ottenere l'estrazione più completa di sostanze preziose dal materiale, aiuta il loro esaurimento mediante clorazione, centrifugazione o azione elettrica.
Nonostante il miglioramento delle tecnologie, il metodo principale per ottenere scorie nella metallurgia ferrosa è il processo di fusione dei metalli in un altoforno o in un forno a focolare aperto. In questo caso la raccolta dei rifiuti viene effettuata per il minor peso specifico. La scoria galleggia sopra la superficie della ghisa e viene rimossa attraverso uno speciale foro per il rubinetto. Con il metodo di fusione a focolare aperto, i rifiuti si accumulano anche sopra la massa liquida di acciaio, la loro raccolta non è difficile.
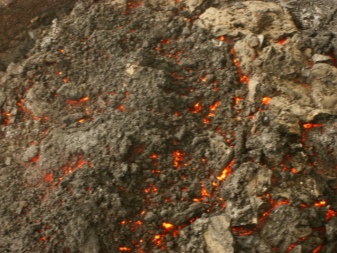
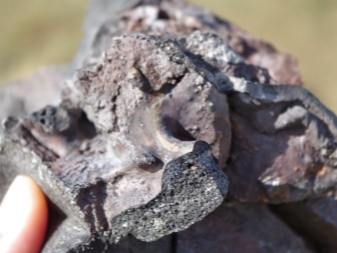
Visualizzazioni
La classificazione principale delle scorie metallurgiche si basa sui metodi della sua produzione e composizione. Sono loro che determinano quale sarà l'ulteriore uso del materiale. La divisione di base distingue tra rifiuti della metallurgia ferrosa e non ferrosa. Il secondo gruppo non è troppo numeroso, contiene una quantità significativa di ossidi di ferro con impurità di calcio e magnesio e nella composizione sono presenti anche impurità più preziose.
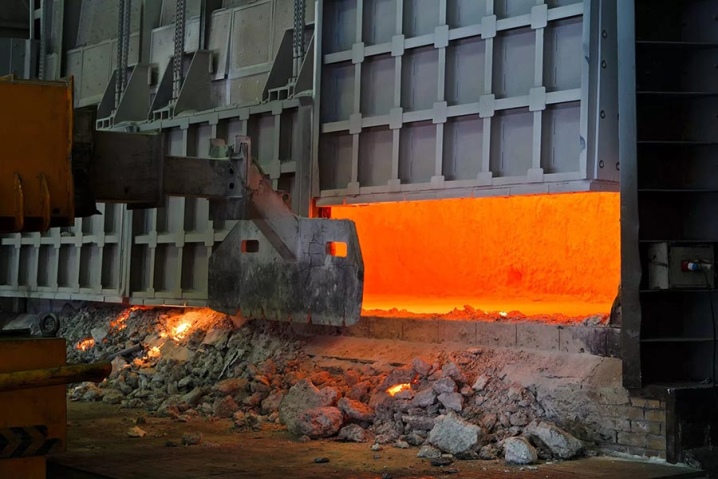
Il peso specifico di tali rifiuti è molto più elevato e richiedono un ulteriore esaurimento.
I gruppi di scorie ottenute nella produzione di metalli ferrosi sono più diversificati. Si dividono in 4 tipologie.
- Ferrolega. Formata durante la fabbricazione delle leghe corrispondenti. Oltre al ferro, tali scorie contengono silicio, manganese, cromo e altri tipi di impurità.
- Cupola. Ottenuto dalla fusione della ghisa in cubilotti - forni speciali. Sono costituiti dal flusso formato, coke, bruciato, cenere e prodotti di ossidazione del metallo. La proporzione di ossidi in essi raggiunge il 90%. Il prodotto risultante ha un'acidità superiore al 3%, rilascia minerali, particelle vetrose di alluminio-silicio.
- Produzione di acciaio. Sono ottenuti per fusione aperta dell'acciaio, indipendentemente dal tipo di unità. Si tratta di ossidi a bassa densità, privi di composti volatili, spesso con una proporzione significativa di contaminanti. Le scorie di questo tipo sono caratterizzate da un alto contenuto di prodotti di ossidazione di ferro e manganese.
- Dominio. Il tipo più comune ha una struttura di silicato o alluminosilicato. A seconda della composizione chimica, al raffreddamento, la scoria acquisisce una struttura pietrosa, dalla quale si ottiene successivamente pietrisco o altro materiale da costruzione, ma può anche sbriciolarsi in polvere. Per determinare lo scopo successivo del materiale, viene utilizzato uno speciale sistema di controllo della qualità.
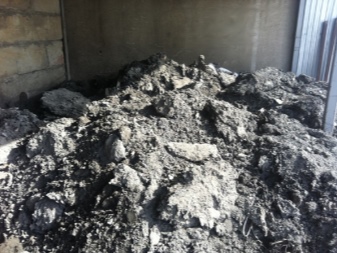
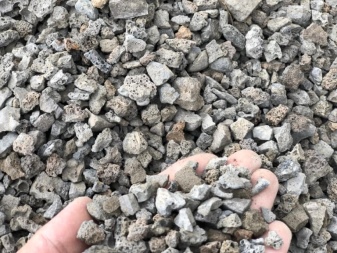
Secondo la loro composizione, le scorie della metallurgia ferrosa dopo il raffreddamento sono divise in rocce in decomposizione e non in decomposizione. Il secondo gruppo assume la forma di formazioni rocciose. Le varianti in decomposizione sono generalmente suddivise in categorie in base alla loro composizione minerale.
Le opzioni più comuni sono:
- silicato: quando riciclati, si disintegrano in fini particelle polverose;
- calcareo - schiacciato in briciole di diverse dimensioni;
- manganese - dissolvenza in un ambiente umido;
- ferroso - soggetto a fessurazioni sotto l'influenza dell'umidità.
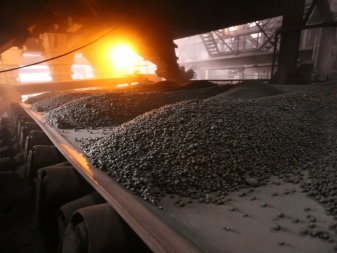
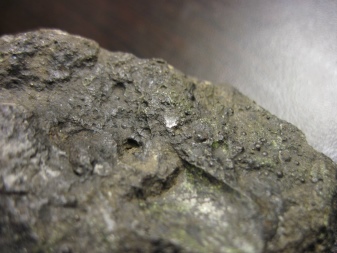
Le scorie, che non si decompongono sotto l'influenza dell'ambiente esterno, vengono utilizzate come base per la produzione di pietrisco e altri tipi di pietra da costruzione. A seconda del metodo di lavorazione, vengono raffreddati e frantumati con metodo semisecco in appositi fusti o sottoposti ad un effetto "bagnato" di un forte getto d'acqua.
In questo caso, il materiale viene immediatamente frantumato nel processo di uscita dall'altoforno e quindi solo soffiato per l'essiccazione e il raffreddamento finale.
Ambito di applicazione
La scoria granulata - scarto della fusione in altoforno di metalli ferrosi - è la più accessibile per ulteriori lavorazioni. Il loro ruolo nel settore delle costruzioni difficilmente può essere sopravvalutato. Il materiale è una fonte di pietrisco, più economico della pietra naturale. Il prodotto finito viene utilizzato:
- per la costruzione di strade - come lettiera;
- nella produzione di manufatti in calcestruzzo;
- in agricoltura, come drenaggio per il suolo;
- nella produzione di calcestruzzo, come aggregato.
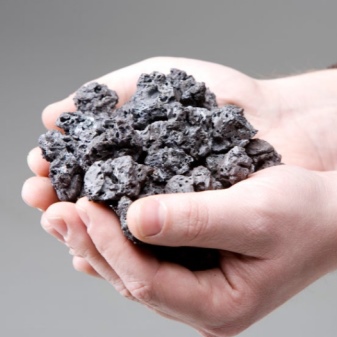
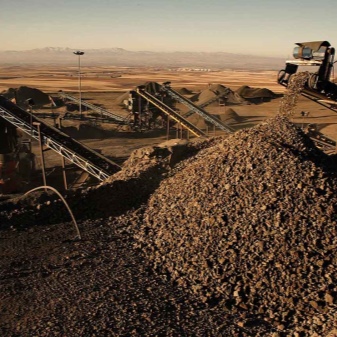
Le scorie ottenute nella produzione di ferroleghe e nella produzione di acciaio vengono aggiunte al cemento sotto forma di impurità polverose. Tale composizione acquisisce una maggiore resistenza chimica. In combinazione con il clinker di cemento Portland, è possibile migliorare ulteriormente le proprietà fisiche del materiale. Le scorie granulari mescolate con vetro liquido o soda vengono utilizzate nella produzione di miscele di calcestruzzo in grado di indurire a basse temperature.
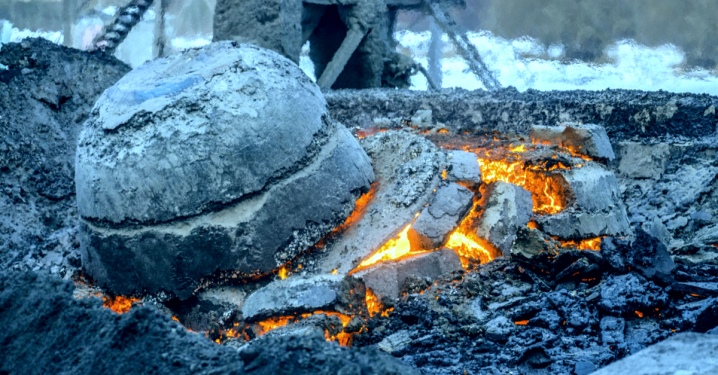
Quando si colano le scorie, è possibile ottenere prodotti finiti: lastre per pavimentazione e cordoli, rivestimenti per pavimenti interni. Inoltre, questo metodo consente di creare tubi e raccordi per loro, decorazione della facciata. I costi di produzione sono significativamente ridotti e, in termini di caratteristiche, il materiale finito non è inferiore alle controparti tradizionali in metallo o cemento armato. La colata avviene mediante stampaggio di scorie fuse.
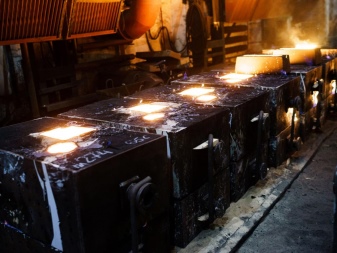
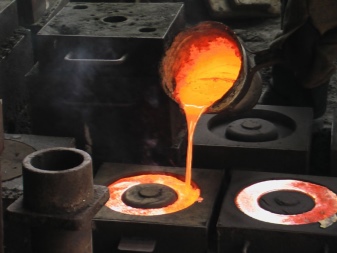
La lana minerale può essere ottenuta dall'altoforno viscoso, dalla fusione dell'acciaio, dalle materie prime a cupola. Per questo, la composizione riscaldata allo stato liquido viene inviata a macchine trafilatrici per formare fibre.
Le lastre così ottenute possono essere molto dure o piuttosto morbide, avere una struttura elastica, densa. A causa dei polimeri sintetici e dei leganti bituminosi, mantengono le loro proprietà per lungo tempo.
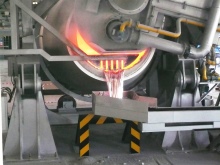
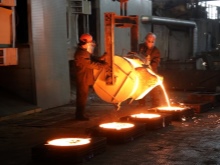
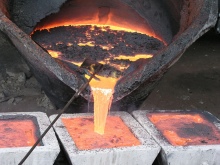
Il commento è stato inviato con successo.