Tutto sulle scorie d'altoforno
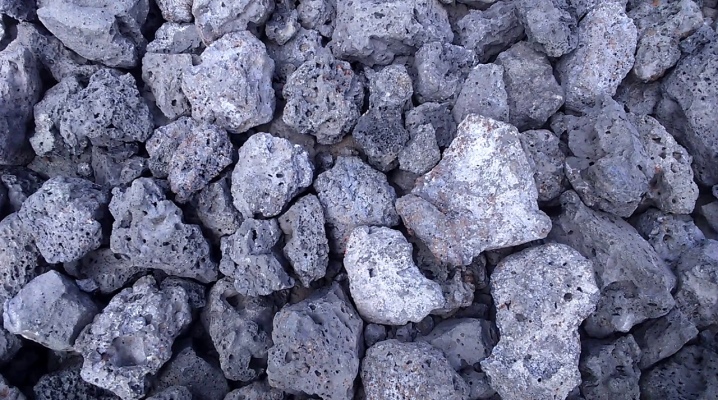
È molto importante che i consumatori scoprano di cosa si tratta: scorie di altoforno. La corretta caratterizzazione profonda non può limitarsi alla conoscenza della densità della scoria granulare, con le sue differenze rispetto alla siderurgia, con un peso di 1 m3 e una composizione chimica. È imperativo scoprire qual è l'uso dei vagli di frantumazione e quali sono i tipi particolari di tali prodotti.
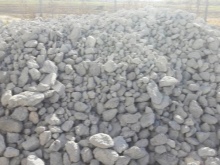
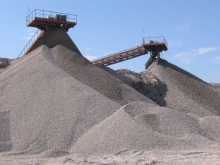
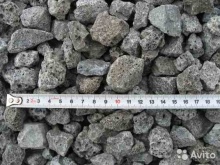
Cos'è?
Il nome "scorie d'altoforno" si riferisce ad un tipo specifico di massa di pietra artificiale. Appaiono come un sottoprodotto della produzione della fusione dei metalli in altoforno - da cui il nome comune. La roccia di scarto si fonde con i flussi contenuti nella carica, ed è così che appaiono i prodotti di scoria.
Se il processo di altoforno viene eseguito rigorosamente secondo la tecnologia, la scoria sembra un prodotto leggero (grigio chiaro, con note gialle, verdastre e alcune altre). Se il produttore viola la tecnologia stabilita, appare un altro colore: il nero, questo indica un'alta concentrazione di ferro nei prodotti fabbricati.
Anche la trama della massa della scoria differisce entro ampi limiti. Opzioni conosciute:
- simile alla pietra;
- simile al vetro;
- simile alla porcellana.
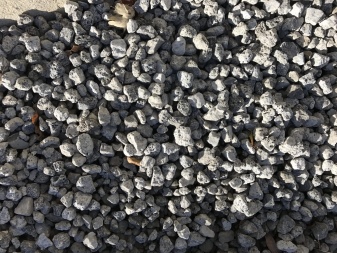
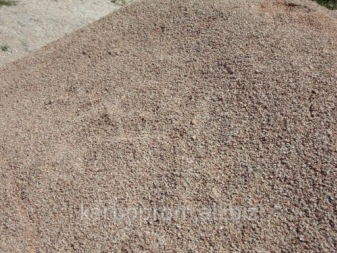
Composizione e caratteristiche
Poiché anche in un'impresa che riceve materie prime da una cerchia stabile di fornitori, le sfumature tecnologiche possono cambiare, è naturale che in diversi casi anche le proprietà e la composizione delle scorie siano significativamente diverse. Spesso puoi leggere che questo prodotto è chimicamente vicino al cemento. E questa affermazione non è priva di fondamento. Tuttavia, c'è leggermente meno ossido di calcio nella massa della scoria, ma c'è chiaramente più biossido di silicio, ossido di alluminio e altri composti simili.
Si dovrebbe notare che gli ossidi sono solitamente presenti non in forma pura, ma come parte di altri composti. Inoltre, poiché il processo tecnologico implica un forte raffreddamento della massa lavorata, la composizione chimica della scoria include vetro alluminosilicato. Ha un'impressionante capacità di reagire con altre sostanze. Un altro argomento importante è il peso specifico di 1 m3 di loppa d'altoforno, che è anche la densità apparente, infatti (a volte questi concetti sono diluiti, ma rimangono comunque strettamente interconnessi per ovvi motivi). Questa cifra può variare da 800 a 3200 kg, a seconda della materia prima, dei metodi di lavorazione e di altre sottigliezze tecnologiche.
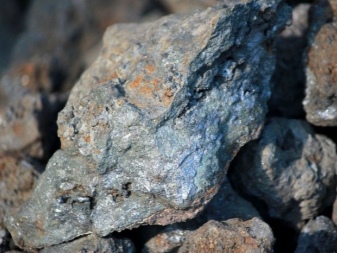
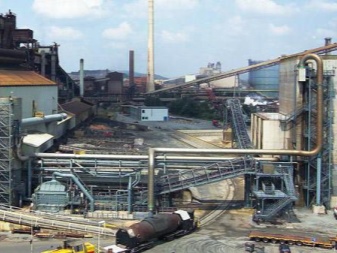
In pratica, però, la maggior parte delle scorie pesa comunque non meno di 2,5 e non più di 3,6 g per 1 cm3. A volte è persino più leggero del metallo fuso. Non c'è da stupirsi, altrimenti sarebbe stato impossibile separare in modo chiaro e competente la massa di scorie dal prodotto principale degli impianti metallurgici. Anche lo speciale GOST 3476, adottato nel 1974, si applica alle scorie d'altoforno.
Nota: questa norma non copre i prodotti derivati da ferroleghe e minerali di magnetite di qualsiasi origine.
La norma normalizza:
- il contenuto di ossido di alluminio e alcune altre sostanze;
- la proporzione di frammenti che non hanno subito una granulazione completa;
- dimensione nominale di un lotto standard (500 tonnellate);
- requisiti per i campioni di prova prelevati da ciascun lotto consegnato separatamente;
- procedura di ripetizione del test per indicatori discutibili o ambigui;
- requisiti per lo stoccaggio e la movimentazione dei prodotti finiti.
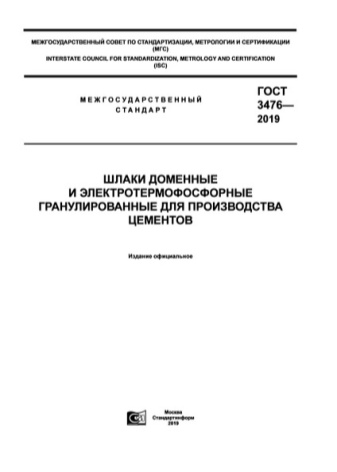
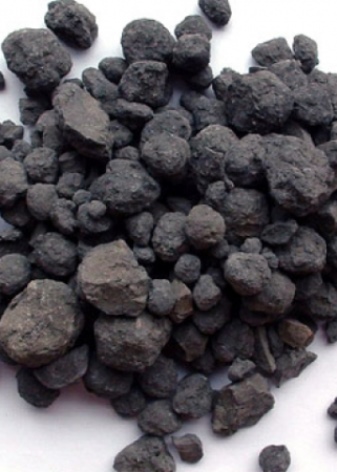
Il livello standardizzato di conduttività termica delle scorie d'altoforno è preso pari a 0,21 W / (mC). Questo è un indicatore abbastanza decente, e ancora peggiore di quello della lana minerale. Pertanto, tale isolamento dovrà essere inserito in uno strato più spesso. Nelle caratteristiche del lotto di merce consegnato, deve essere indicato un parametro come la friabilità. Maggiore è la proporzione di grani lisci, minore "adesione" tra loro e anche più difficile è preparare una soluzione e tenere insieme la massa.
È utile notare, Sfortunatamente, la compatibilità ambientale delle scorie d'altoforno è altamente discutibile. Il suo utilizzo a diretto contatto con l'ambiente, ad esempio nella costruzione di strade, provoca gravi rischi, anzitutto contribuisce alla diffusione dei metalli pesanti. Ma se escludiamo l'erosione della massa da parte del suolo, dello scioglimento dell'acqua e delle precipitazioni, il problema è ampiamente risolto. Pertanto, non vale assolutamente la pena rinunciare all'uso di prodotti di scoria - in ogni caso, è meglio che buttarlo via direttamente. Tuttavia, bisogna prestare attenzione alle condizioni d'uso.
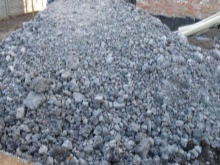
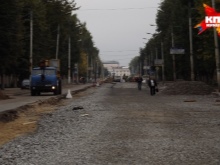
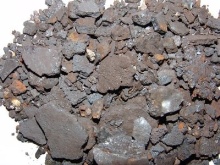
Differenze dalle scorie siderurgiche
La principale specificità è che un tale prodotto è ottenuto utilizzando una tecnologia completamente diversa. E quindi la sua composizione chimica, e quindi, ovviamente, le sue proprietà, sono molto diverse. I rifiuti della fusione dell'acciaio sono più densi e ovviamente non adatti come semplice riempitivo minerale o isolante. ma a volte è usato come zavorra nella costruzione di strade o come aggregato per miscele di asfalto.
Gli esperimenti stanno dando risultati promettenti, ma ancora la classica scoria d'altoforno rimane un prodotto più conveniente e attraente.
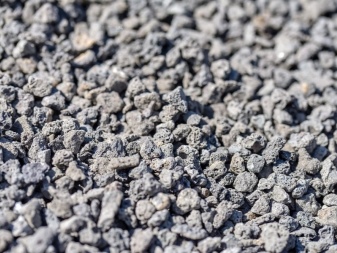
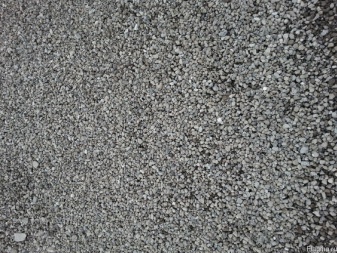
Tecnologia di produzione
La produzione di scorie è associata alla fusione in un forno speciale, ad esempio la ghisa. La sostanza di cui abbiamo bisogno lascia l'altoforno, essendo riscaldata ad almeno 1500 gradi. Pertanto, per poter lavorare con esso, è necessario raffreddare la scoria. Sarebbe troppo lungo aspettare che questo avvenga naturalmente. Pertanto, praticano:
- gonfiore (o altrimenti, fornitura di acqua fredda);
- soffiaggio con getti d'aria;
- frantumazione o macinazione su attrezzature speciali.
Va notato che il metodo di lavorazione influisce direttamente sulla composizione e sulle caratteristiche del prodotto finito. Tutti i granulatori lo sanno e quindi tengono conto di un tale momento in cui viene posto un determinato compito. Ad esempio, con il raffreddamento ad aria, nella scoria prevarranno i silicati e gli alluminosilicati. In alcuni casi, la scoria viene anche frantumata meccanicamente: questa procedura viene utilizzata mentre è ancora liquida o dopo una parziale solidificazione. I pezzi di grandi dimensioni vengono trasformati in piccoli grani in modo tale da migliorare ulteriormente le prestazioni di lavoro e migliorare la qualità del prodotto finito.
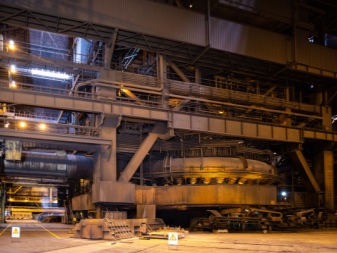
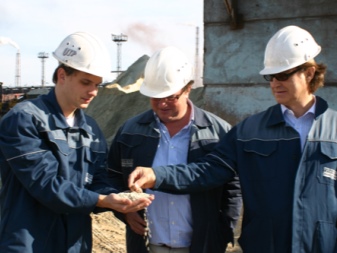
Certo, nessuno produce di proposito scorie d'altoforno. Sottolineiamo ancora che questo è sempre solo un sottoprodotto della produzione metallurgica.
La produzione di granuli può essere effettuata con vari metodi, utilizzando dispositivi specifici. Sono noti sistemi per la granulazione a umido e semisecco. Nel metodo umido, la scoria viene caricata in vasche di cemento armato riempite d'acqua.
È consuetudine dividere le piscine in più settori. Questo approccio garantisce la continuità della procedura di produzione. Non appena la materia prima riscaldata viene versata in una parte, l'altra è già pronta per scaricare la scoria raffreddata. Nelle imprese moderne, lo scarico viene effettuato da gru a benna. La quantità di acqua residua dipende dalla porosità e la porosità stessa è determinata dalle caratteristiche del processo di raffreddamento.
Per produrre una scoria semisecca, di solito ricorrono alla frantumazione meccanica. Un effetto simile si ottiene lanciando nell'aria scorie raffreddate, ma non ancora completamente solidificate. Di conseguenza, il materiale è più denso e più pesante del materiale granulato umido. Il contenuto di umidità del prodotto finito sarà del 5-10%. Maggiore è la temperatura di fusione, più leggero sarà il prodotto finito.
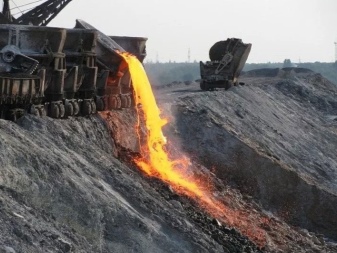
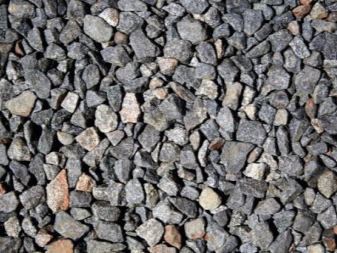
Visualizzazioni
La loppa metallurgica d'altoforno è ottenuta dalla fusione della ghisa. A seconda della frazione e della densità apparente, un tale prodotto è considerato un prodotto poroso o denso. Il pietrisco con una densità apparente specifica inferiore a 1000 kg per 1 m3 e la sabbia con una densità apparente specifica inferiore a 1200 kg per 1 m2 sono considerati porosi.
Un ruolo importante è svolto dal cosiddetto modulo di basicità, che determina la natura alcalina o acida della sostanza.
Durante il processo di raffreddamento, una sostanza può:
- mantenere amorfo;
- cristallizzare;
- subiscono una parziale cristallizzazione.
La scoria macinata viene prodotta da gradi granulari mediante macinazione aggiuntiva. A seconda del target, è possibile aggiungere un additivo idrofobo. Il prodotto di solito soddisfa le specifiche del 2013. Le scorie di discarica vengono generate come rifiuti. Il suo valore direttamente per la produzione metallurgica non è elevato, tuttavia stanno già emergendo tecnologie per la lavorazione della massa di discarica.
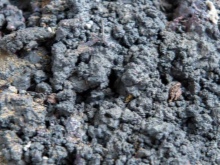
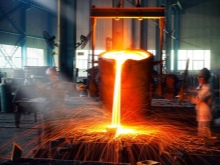
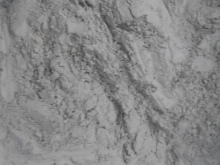
Ambito di applicazione
La scoria di altoforno è ampiamente utilizzata. Il suo principale campo di applicazione è la produzione di materiali da costruzione. Finora, quest'area è sviluppata in modo non uniforme in diverse regioni del paese. Tuttavia, la riduzione della distanza di trasporto dei materiali da costruzione verso i cantieri non può che essere accolta con favore. All'estero, non solo le scorie di altoforno, ma anche le scorie di produzione dell'acciaio vengono utilizzate nella costruzione di strade, ma questo è già un argomento per una conversazione separata.
Un semplice prodotto versoio è in grado di impostare rapidamente, il che lo rende analogo al cemento. L'uso di una tale massa nello scarico delle superfici stradali si sta gradualmente espandendo. Inoltre, in molti luoghi, cercano di rafforzare i cuscinetti di supporto delle fondamenta. Ci sono sviluppi sull'uso dei vagli di frantumazione come componente principale del calcestruzzo. Ci sono già una serie di pubblicazioni in cui questa esperienza è incoraggiata.
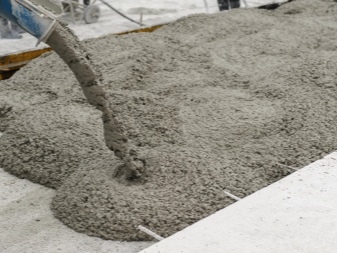
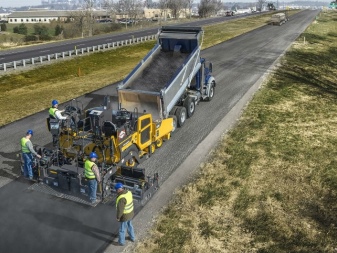
La scoria frantumata viene prodotta frantumando la scoria di scarico e facendola passare attraverso i vagli. L'applicazione specifica è influenzata principalmente dalla frazione di materiale. L'uso di un prodotto come:
- riempitivo di miscele di calcestruzzo durevoli;
- cuscini di zavorra sui binari ferroviari;
- mezzi per rafforzare le piste;
- materiale per banchina e ormeggio;
- mezzi di sistemazione dei siti.
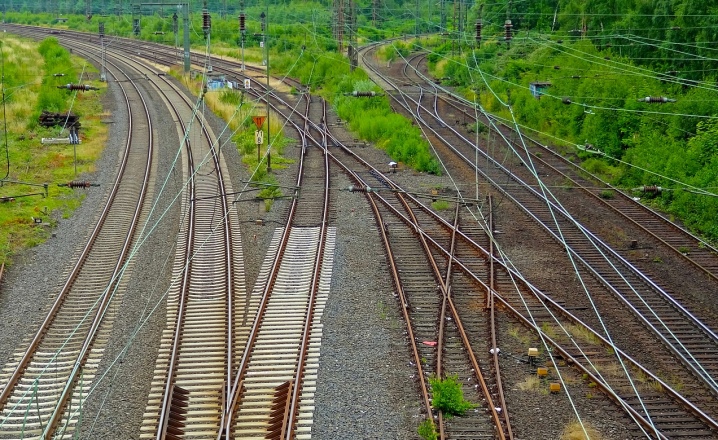
La scoria granulare viene utilizzata per ottenere blocchi di cenere. È anche necessario per l'isolamento termico. A volte per il drenaggio viene utilizzata la scoria d'altoforno: in questa capacità si degrada rapidamente, si trasforma in sabbia, ma funziona ancora correttamente. La massa granulare può essere utilizzata anche per la sabbiatura.
Questa applicazione è molto comune e il prodotto richiesto è offerto da molti produttori leader.

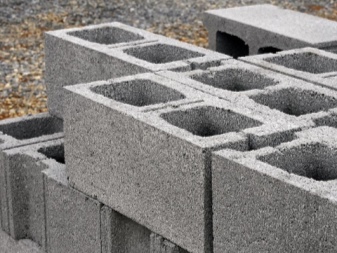
Il commento è stato inviato con successo.