Solai leggeri: caratteristiche, dimensioni e utilizzo
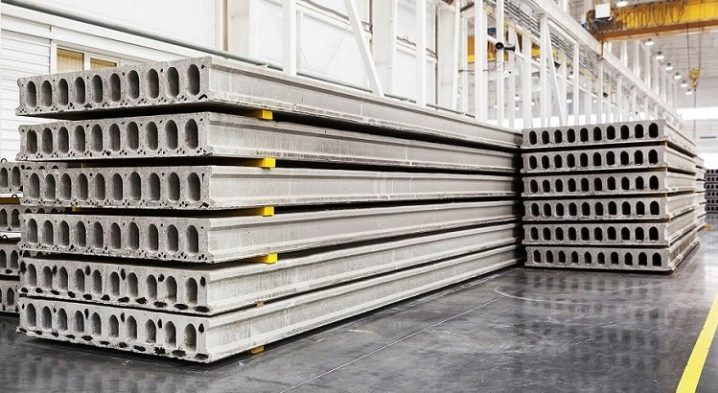
I ricercatori della struttura del palazzo a Carskoe Selo affermano che i nostri compatrioti usavano il cemento armato già nel 1802. Tuttavia, il materiale fu brevettato nel 1847 da un normale giardiniere di Versailles. All'inizio del XX secolo, l'ingegnere, architetto, designer e inventore russo Livchak Fedor Osipovich apprezzò le ampie possibilità di utilizzo di un materiale come la bentonite. Nel 1909 fu eretto il primo edificio dei pannelli "Livchak".
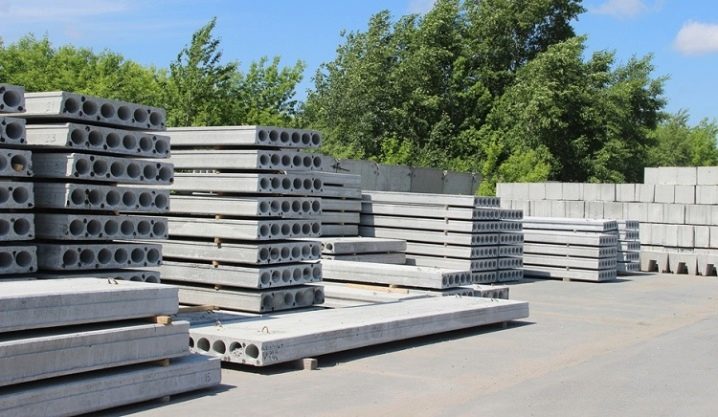
Cos'è?
La sovrapposizione è ciò che nella vita di tutti i giorni viene chiamato pavimento e soffitto. Le solette leggere sono lastre di cemento armato rettangolari a forma di U o piatte. All'interno di quest'ultimo, ci sono vuoti passanti lungo l'intera area.
Durante la costruzione delle strutture, ci sono solo 2 tipi di piani: monolitici (vengono armati e colati con malta cementizia direttamente in cantiere) e prefabbricati (assemblati da lastre finite, e gli interstizi tra loro vengono riempiti, se necessario, con armature e calcestruzzo).
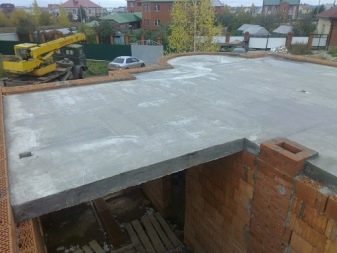
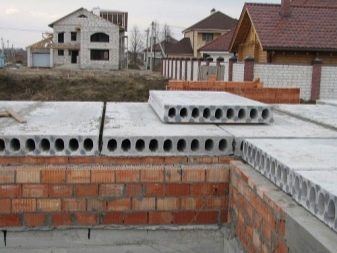
A differenza dei pavimenti monolitici, le strutture prefabbricate hanno i loro vantaggi.
- Sono più economici a causa del basso consumo di materiali durante la produzione a causa dei vuoti, sia per il produttore che per l'acquirente.
- Montaggio più facile e veloce. Hanno un'elevata resistenza grazie agli irrigidimenti esistenti e una forma rettangolare uniforme.
- Per l'installazione, è sufficiente noleggiare una gru e imbracature, perché i blocchi sono leggeri e non molto larghi.
- I vuoti nelle lastre riducono il livello di rumore e forniscono un isolamento termico aggiuntivo grazie al "cuscino d'aria" risultante.
- In fabbrica, i pannelli sono realizzati con una qualità migliore e più affidabile, poiché gli indicatori sono controllati in ogni fase della produzione.
- Le cavità possono essere utilizzate per varie comunicazioni.
- L'installazione può essere eseguita in tutte le condizioni atmosferiche.
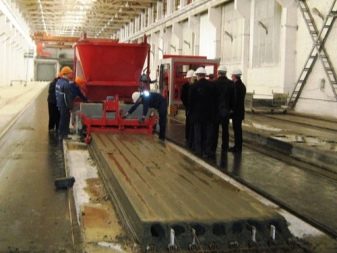
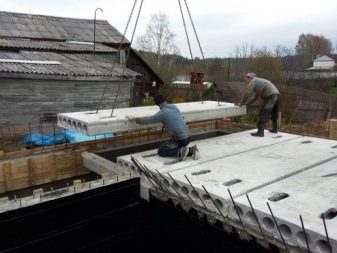
Tuttavia, niente è perfetto. Parametri in base ai quali le lastre prefabbricate sono inferiori ai rivestimenti monolitici:
- l'installazione è impossibile senza l'uso di mezzi di sollevamento;
- il livello di durezza è inferiore;
- ci sono sempre spazi tra le lastre che richiedono un'ulteriore elaborazione;
- la loro durata è insignificante, ma meno, i pavimenti in cemento stanno guadagnando forza solo per circa 50 anni;
- dipendenza dalle dimensioni di fabbrica (una sezione popolare di 1500 mm è disponibile in tutte le nomenclature), quindi a volte è necessario utilizzare elementi aggiuntivi aggiuntivi;
- i blocchi finiti hanno una grande altezza a causa di vuoti o forma (lastre a forma di U);
- sono necessari ulteriori calcoli e elaborazioni.
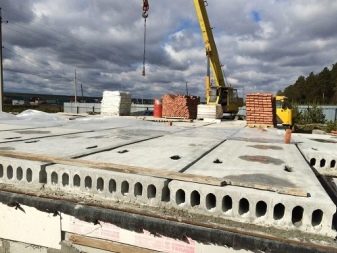
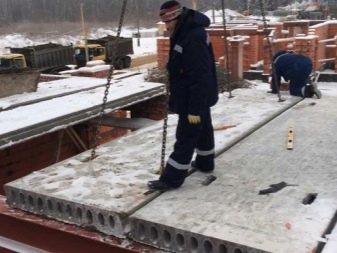
Visualizzazioni
Solo le fabbriche specializzate sono impegnate nella produzione di pannelli leggeri, che oggi in Russia non possono ancora far fronte alla crescente domanda. Questi pavimenti stanno attivamente guadagnando popolarità e riattrezzare la produzione non è un compito facile e richiede anche grandi investimenti.
Pertanto, ci vuole tempo per produrre e consegnare un ordine.
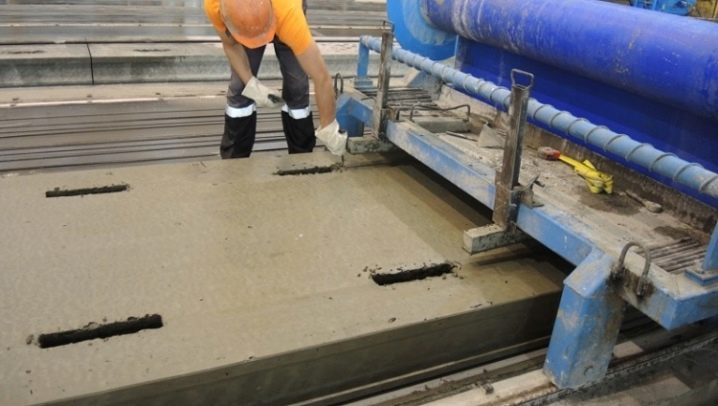
A prima vista, le solette leggere non sono significativamente diverse l'una dall'altra. In effetti, c'è una differenza tra loro, e una grande. Ci sono 4 tipi principali in totale.
- Solai alveolari della serie PC. Per la loro fabbricazione vengono utilizzate sabbia, pietrisco, cemento e armature ordinarie o sollecitate (prima del getto del calcestruzzo, viene tirato con martinetti o elettrotermicamente) in forme metalliche speciali.
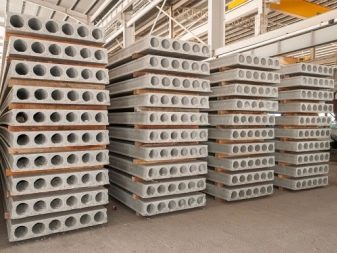
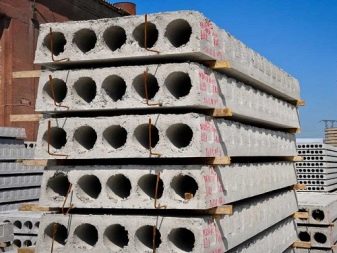
La produzione avviene in più fasi:
- installare rinforzi e elementi di formazione del vuoto;
- gli stampi sono colati con cemento;
- compattazione del calcestruzzo su tavole vibranti;
- avviene il primo trattamento termico;
- effettuare piccole riparazioni, installare spine;
- il prodotto viene cotto a vapore in apposite camere;
- avviene un secondo trattamento termico;
- tagliare i pezzi di rinforzo in eccesso.
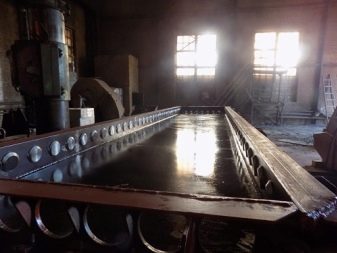

L'armatura può essere posizionata lungo e trasversalmente alla soletta. I vuoti sono rotondi, 127, 140 o 159 mm di diametro. Per aumentare la resistenza, le cavità vengono talvolta riempite di cemento (è possibile ordinare in fabbrica). Per semplificare l'installazione, sono montati 4 anelli di imbracatura lungo il perimetro. L'altezza standard è di 220 mm. Lunghezza - da 1180 a 9700 mm (variabile in passi di 300 mm), larghezza - da 990 a 3500 mm. Carico standard - 600 kg/cm², 800 kg/cm² (su ordinazione può essere aumentato a 1250 kg/cm²).
Non ci sono praticamente restrizioni per quanto riguarda l'applicazione, da un garage a un edificio a più piani.
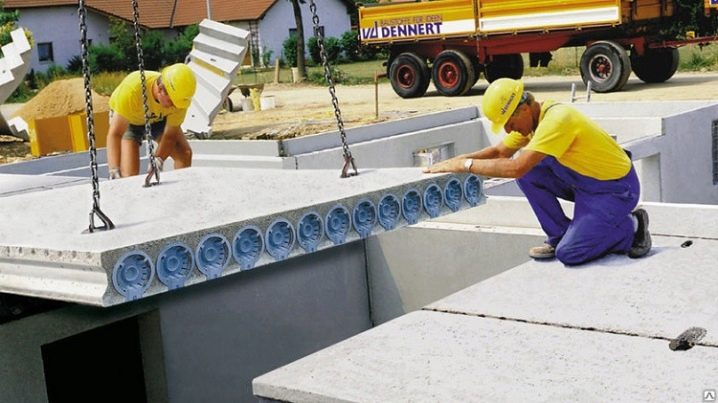
- Solai alveolari della serie PB. L'armatura tesa si trova longitudinalmente. Durante la produzione viene utilizzata la tecnica della formatura continua senza casseforme su lunghe gabbie.
Per questo vengono utilizzate attrezzature speciali e tecnologie speciali:
- estrusione (dall'estrusione inglese - spingere fuori, spremere) ed estrusione combinata con vibrazione (l'estrusore è una macchina in cui la miscela di calcestruzzo viene spremuta e contemporaneamente formata);
- La formazione della spaccatura (dall'inglese split - separazione, biforcazione) è la formazione di fibre combinata con la trombosi (cassaforma laterale di uno splitformer, che a sua volta comprime 2 strati di miscela di calcestruzzo e i formatori di vuoto della soletta creano vibrazioni).
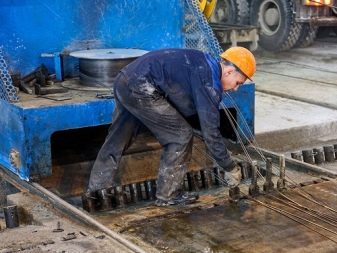
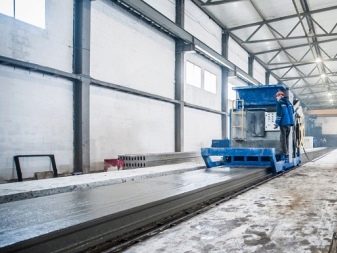
Secondo i parametri specificati, il taglio del nastro risultante viene eseguito da un altro dispositivo. I vuoti hanno una forma semicircolare. Non ci sono anelli di montaggio. L'altezza delle lastre va da 160 a 330 mm, la lunghezza arriva fino a 12000 mm (a seconda dell'ordine può variare con incrementi di 100 mm), la larghezza va da 1000 a 1500 mm. Carico standard - da 300 a 1600 kg / cm². Applicazione - costruzione bassa. A differenza della serie precedente, la lastra può essere tagliata con un angolo di 45 gradi (ci sono più possibilità applicative per quanto riguarda le soluzioni progettuali). Grazie alla lavorazione con macchina levigatrice, la superficie risulta liscia (consente di ridurre il consumo di materiali per il successivo livellamento del pavimento durante le riparazioni).
Qualitativamente, la lastra ha prestazioni più elevate grazie all'utilizzo di nuove tecnologie di produzione.
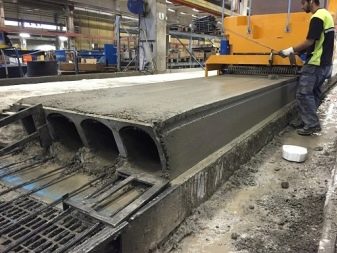
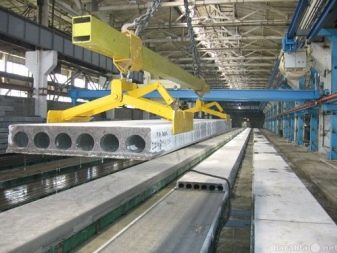
- Placche della serie PNO. Per la produzione vengono utilizzate tecnologie di casseforme e supporti (l'intero processo di produzione è simile alla cassaforma, solo che avviene su supporti fissi). I vuoti sono rotondi e hanno un diametro maggiore rispetto alle lastre di PC. Gli anelli di montaggio non sono sempre disponibili. Il diametro dei vuoti è di 144 mm. Altezza - 160 mm. Lunghezza - da 1580 a 6280 mm, larghezza - da 990 a 1490 mm. Carico standard - da 300 a 1000 kg / cm². Sono utilizzati nella costruzione a vita bassa. Caratteristiche distintive della lastra PNO delle serie PK e PB: a causa dell'aumento del diametro dei vuoti, il peso diminuisce, la produzione diventa più economica e gli irrigidimenti vengono rinforzati, nella produzione vengono utilizzati calcestruzzo più resistente e rinforzi ispessiti.
- Piastre a forma di U a coste. Nella produzione viene utilizzata una rete di rinforzo (le intersezioni sono collegate mediante saldatura). Il calcestruzzo nelle forme preparate viene posato in 2 strati. Ciascuno viene vibrato rigorosamente per 1 e 2 minuti, rispettivamente. Segue il trattamento termico e la successiva rifilatura. Gli anelli di montaggio sono installati. Altezza - da 220 a 600 mm, lunghezza - da 4780 a 18000 mm, larghezza - da 1190 a 3000 mm. Carico standard - da 350 kg / cm². I pannelli nervati sono utilizzati nella costruzione di edifici non residenziali, centrali termiche e sistemi di approvvigionamento idrico.
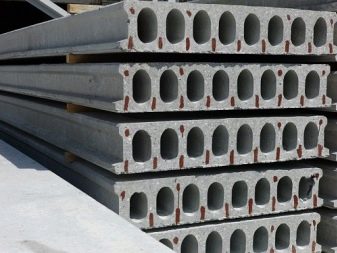
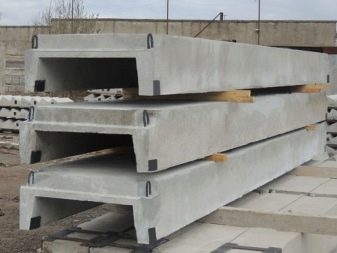
Da quanto sopra, puoi vedere che tutti i solai leggeri differiscono tra loro nei seguenti parametri:
- tipo di sezione: cavo e nervato;
- numero di strati: singolo strato e doppio strato;
- metodo di rinforzo;
- dimensioni;
- carico normativo;
- metodo di preparazione;
- area di applicazione.
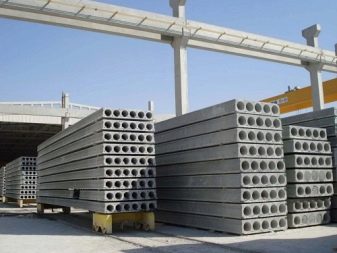
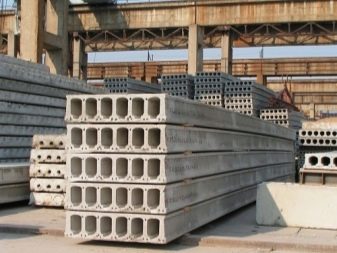
Inoltre, ci sono altre differenze:
- per la produzione vengono utilizzati diversi tipi di calcestruzzo;
- i fori disponibili possono essere di diversi diametri e forme;
- peso diverso.
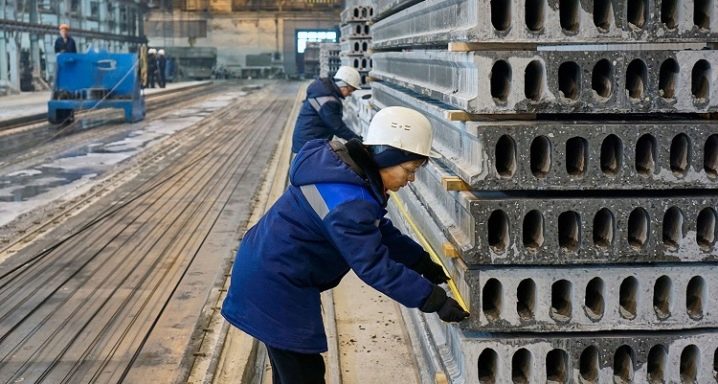
Tecnologia di installazione
Prima di procedere all'installazione del pavimento, vengono redatti i disegni, in stretta conformità con i quali iniziano ad agire. Questo aiuta a trovare il posizionamento ottimale delle piastre, nonché le loro dimensioni. Quando si elaborano i disegni, la cosa principale a cui si presta attenzione sono le pareti portanti. Secondo il progetto finito, sarà possibile calcolare la lunghezza e la larghezza richieste dei pannelli al fine di ridurre al minimo gli spazi tra loro.
Il processo di installazione stesso è il seguente:
- i blocchi vengono sollevati e impilati utilizzando un'autogru;
- per una connessione forte e per evitare la formazione di spazi vuoti, i blocchi vengono fissati su una malta cementizia;
- secondo lo schema di posa standard, la lastra dovrebbe andare 120-150 mm sulla parete di supporto;
- i pannelli sono fissati tra loro mediante barre di acciaio, anelli di montaggio e saldatura;
- le cuciture vengono colate con cemento (se necessario, viene eseguito il rinforzo).
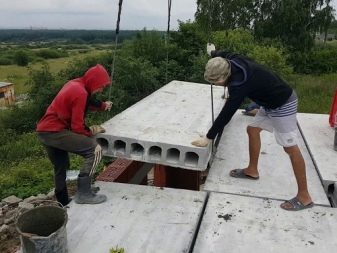
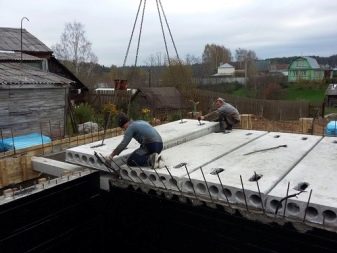
Questo schema prevede anche la sigillatura delle estremità, che impedirà il congelamento della casa, che viene eseguita come segue:
- è necessario riempire i vuoti con lana minerale 200-300 mm;
- riempire i vuoti con calcestruzzo leggero 120-200 mm;
- chiudere con tasselli in cemento;
- prendere un normale mattone rosso nel mortaio e sigillare la superficie con esso.
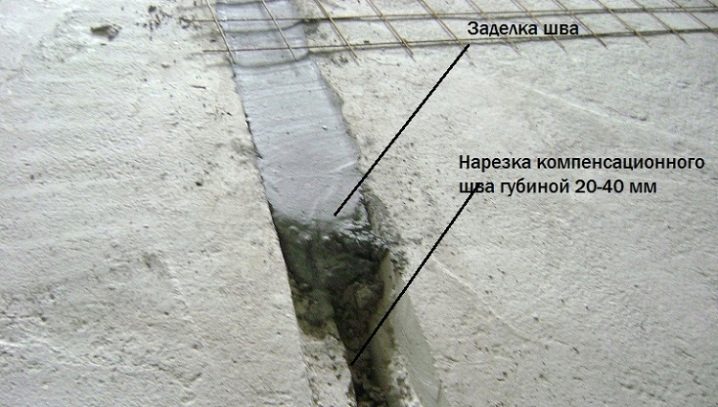
Regole di selezione
Con qualsiasi azione, vuoi sempre risparmiare denaro e non perdere qualità. In una questione come la costruzione, l'entità del risparmio è significativa, così come la responsabilità del risultato. Sulla base delle conclusioni di cui sopra, non sarà difficile trarre: per la costruzione a pochi piani, la piastra di copertura della serie PNO è l'ideale.
La sua altezza e la superficie liscia consentono non solo di risparmiare sui materiali di finitura, ma anche di aumentare l'altezza del soffitto di almeno 60 mm. I vuoti più grandi migliorano l'isolamento termico e acustico e le nervature di irrigidimento, riducono il peso e riducono i costi di produzioneda qui il costo della stufa. Inoltre, le cavità consentono di nascondere non solo il cablaggio, ma quasi tutte le comunicazioni. I blocchi sono resistenti alle variazioni di temperatura e umidità.
Gli svantaggi includono la necessità di un dispositivo di sollevamento.
I tempi di consegna dei prodotti finiti possono essere lunghi e, naturalmente, dovrai occuparti di calcoli e stesura di disegni, tenendo conto delle peculiarità della progettazione degli edifici.
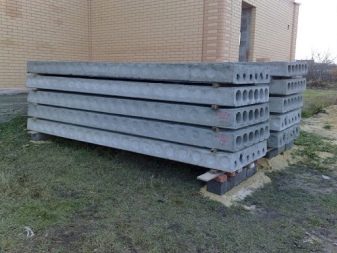
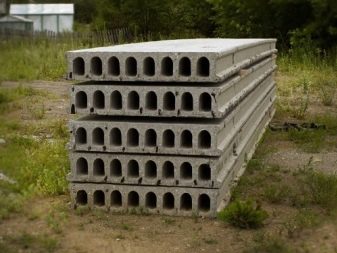
Puoi scoprire come posare uniformemente i solai guardando il video qui sotto.
Il commento è stato inviato con successo.